Common interests
Using a new refrigerated platform with a direct network connection, DACHSER Food Logistics in Neuss is helping three food producers get closer to their customers in Germany and Europe—faster.
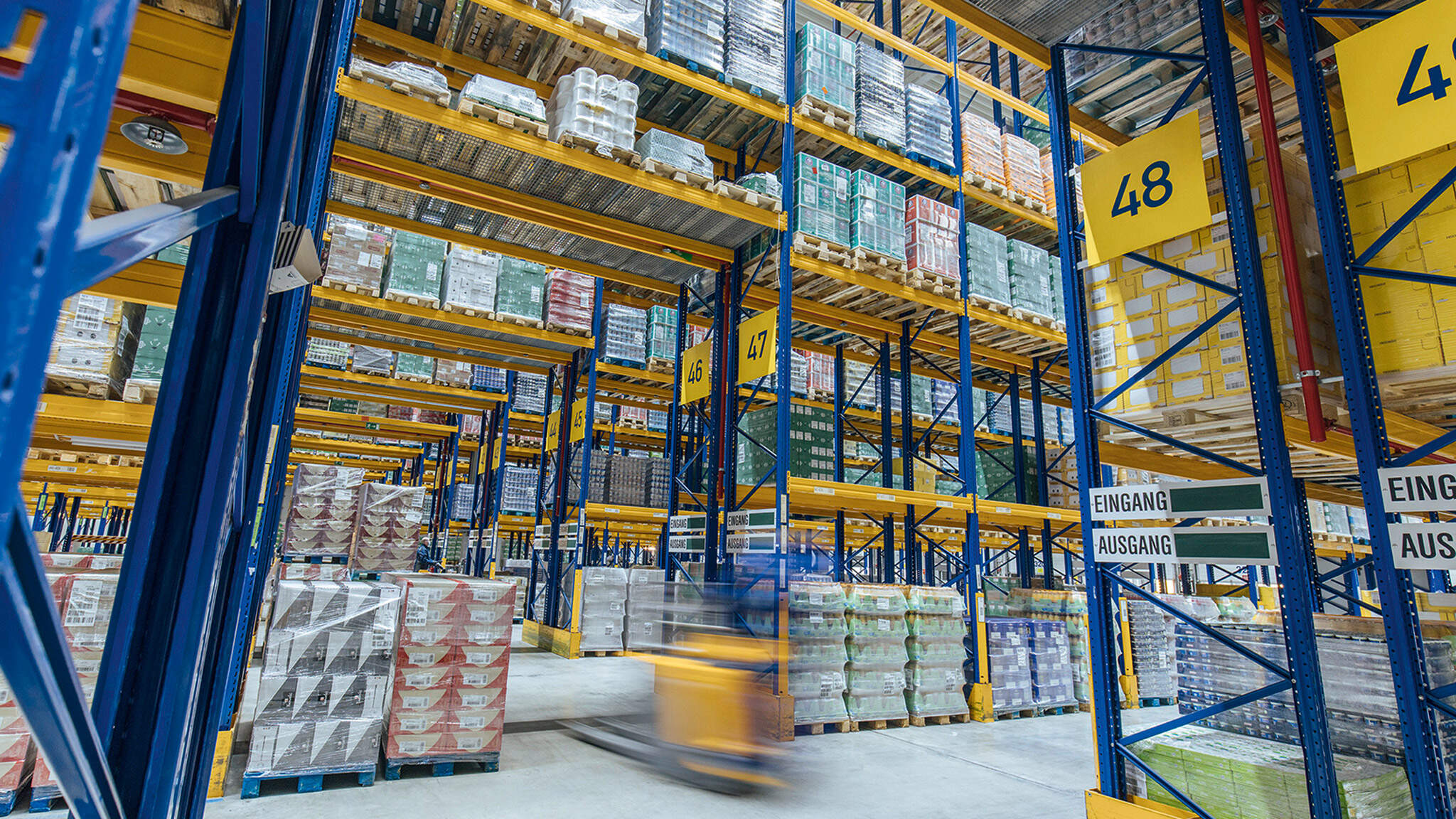
When life gets really hectic, many people turn to endurance sports as a means of clearing their head, getting some fresh air, and gathering new inspiration and energy along the way. That’s why Stefan Behrendt enjoys spending what little free time he has on his racing bike. Over the past two years, the General Manager of DACHSER’s Niederrhein logistics center led his team to victory in a different high-performance “sport”: establishing a universal logistics portfolio for fresh food producers in the middle of a pandemic.
DACHSER invested approximately EUR 2.5 million in converting a warehouse in Neuss near Düsseldorf, furnishing it with a chilled storage area large enough to accommodate almost 26,000 pallets. Amid the complicated conditions of the pandemic, the company hired and onboarded 80 employees. Alfred Miller, Managing Director DACHSER Food Logistics: “We’re ideally placed to bundle large volumes of goods from the warehouse with those from distribution customers in the region and to supply most central warehouses operated by German retail chains directly from the source. In this way, we’ve raised food logistics efficiency to a whole new level.” Miller says that it all hinges on how the different variables are combined: “We provide logistics chains that are both ultra-efficient and reliable, capable of handling large volumes and withstanding the fluctuations that are typical for this sector. We make senders’ lives easier by handling much of the order processing and service ourselves. And finally, there’s our highly digitalized information logistics services that accompany every shipment—all from a single source.”
Learning from everyday practice to benefit everyday practice
Behrendt says that in 2019, the time had come to turn a long-held dream into a reality. DACHSER’s Niederrhein logistics center is located in a metropolitan area that is home to over ten million people. Behrendt recalls receiving requests from three major food producers at roughly the same time, each asking DACHSER to take over temperature-controlled warehousing services: dairy product companies Arla and Ornua (known for the Kerrygold brand) and fresh juice producer Valensina.
"Bringing three food companies together on a refrigerated platform means synergies for everyone."
“Both Ornua and Valensina had already been DACHSER distribution customers for many years and were looking for a complete logistics solution. Danish dairy giant Arla, which operates production facilities all over Europe, became a new warehouse customer,” Behrendt says. “We bundled these requests into a large-scale project and developed a concept that would bring the three companies together under one roof.” The scale of the new business put the branch in a position to combine the volumes of goods from the multiuser warehouse with the existing volumes of distribution customers in the region, pooling them into direct transports to retailers. “This new refrigerated platform allows us to supply around 70 percent of all central warehouses belonging to retail chains in Germany, the Netherlands, Belgium, and Austria on a daily basis without the need for additional transit terminals,” Behrendt says.
He also notes that by storing their inventories so close to the network, customers are able to respond quickly to last-minute orders, which is ideal for senders that need short turnaround times for fresh products with short shelf lives.

A compelling comprehensive package
At Arla Foods Germany, both Andy Johnson, Director Logistics, and Ann-Katrin Gieß, Senior Procurement Category Manager, Logistics, say that with DACHSER as their system service provider for food business, their company is perfectly positioned: “DACHSER’s comprehensive package, which includes warehousing services at its Neuss location and very frequent deliveries to our retail customers via its robust transport network, had us convinced from the word go.” The same can be said for DACHSER’s emphasis on IT, which ensures transparency along the entire supply chain.
“The digitalization of the supply chain has come a long way in the past few years and this trend is set to continue. There’s still a lot of potential to be tapped,” says Jürgen Retzlaff, Head of Logistics at Ornua Deutschland GmbH. He points out that the advantages of working with DACHSER extend beyond IT-based flexibility in dealing with interconnected schedules and high market volatility. Bundling shipments within the supply chain leads to environmental sustainability.
This is also a priority for Felix Müller, CFO/COO at the Valensina Group: “Since the refrigerated warehouse logistics platform is state of the art, it promotes efficiency—both for us as a customer and for DACHSER in the multiuser warehouse. In this way it helped Valensina improve its carbon ‘foodprint,’ which is important to our company.”
Expanding the bundling platform for fresh products to the regional level took place in several stages. The majority of the existing warehouse was equipped and modernized to handle products that need to be stored at 0–2 or 2–7 degrees Celsius. Completing the work while the warehouse remained open and relocating or incorporating all three customers under pandemic conditions was extremely challenging. “But at every stage I knew that we could do it. And we did—in fact, we finished ahead of schedule,” Behrendt says, clearly proud of the team effort.
“First we implement, then we optimize. The next stage in the expansion will be the addition of 8,000 refrigerated storage spaces by the end of the year,” Behrendt says. Talks are already underway with other players specializing in dairy products, cold cuts, and convenience food. He and his team are excited: “The greater the challenge, the bigger the fun,” Behrendt says with a wink, adding: “There’s a good chance I’ll be biking a few extra kilometers again this year.”